Last updated on
Yes, closure strips are necessary for metal roofing as they ensure a snug fit between roof panels, preventing leaks and pest intrusion.
Key takeaways:
- Closure strips create a secure seal for metal roofing panels.
- Foam closure strips come in solid and vented variations.
- They contribute to sealing, insulation, and aesthetics of the roof.
- Precision installation ensures waterproof and durable metal roofs.
- Consider factors like profile, material, and maintenance when selecting closure strips.
What Are Foam Closure Strips?
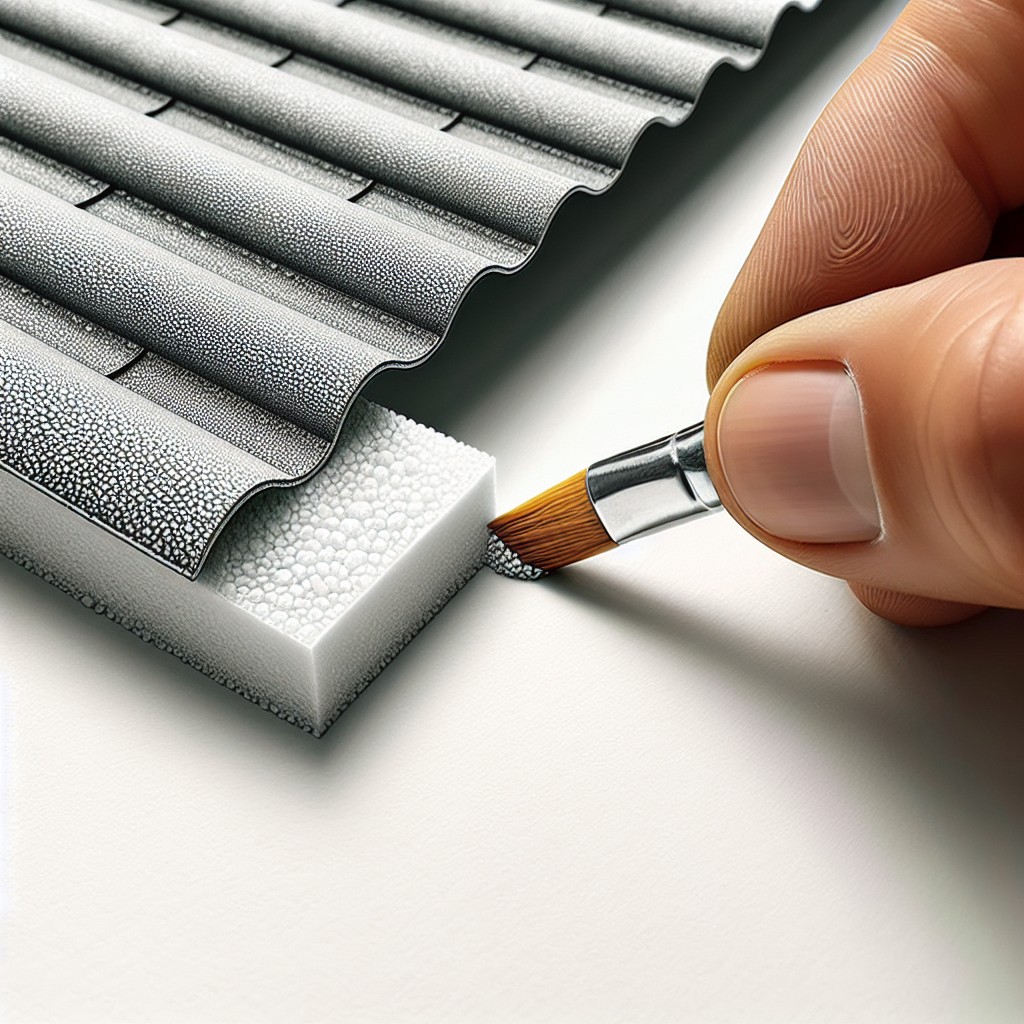
Foam closure strips are designed to fit the profile of metal roofing panels. Constructed from a durable, flexible foam material, these strips serve as a critical seal between the roof panels and the structure. They efficiently fill gaps to prevent insects, dust, and water from entering.
Available in adhesive-backed options for ease of installation, these components enhance overall roof performance. By molding closely to the metal contours, closure strips maintain a consistent appearance and increase the energy efficiency of the building, acting as an additional insulation layer and reducing thermal bridging. Their adaptability to various metal shapes means they are essential for a wide range of roofing designs.
The Purpose of Foam Closure Strips in Metal Roofing
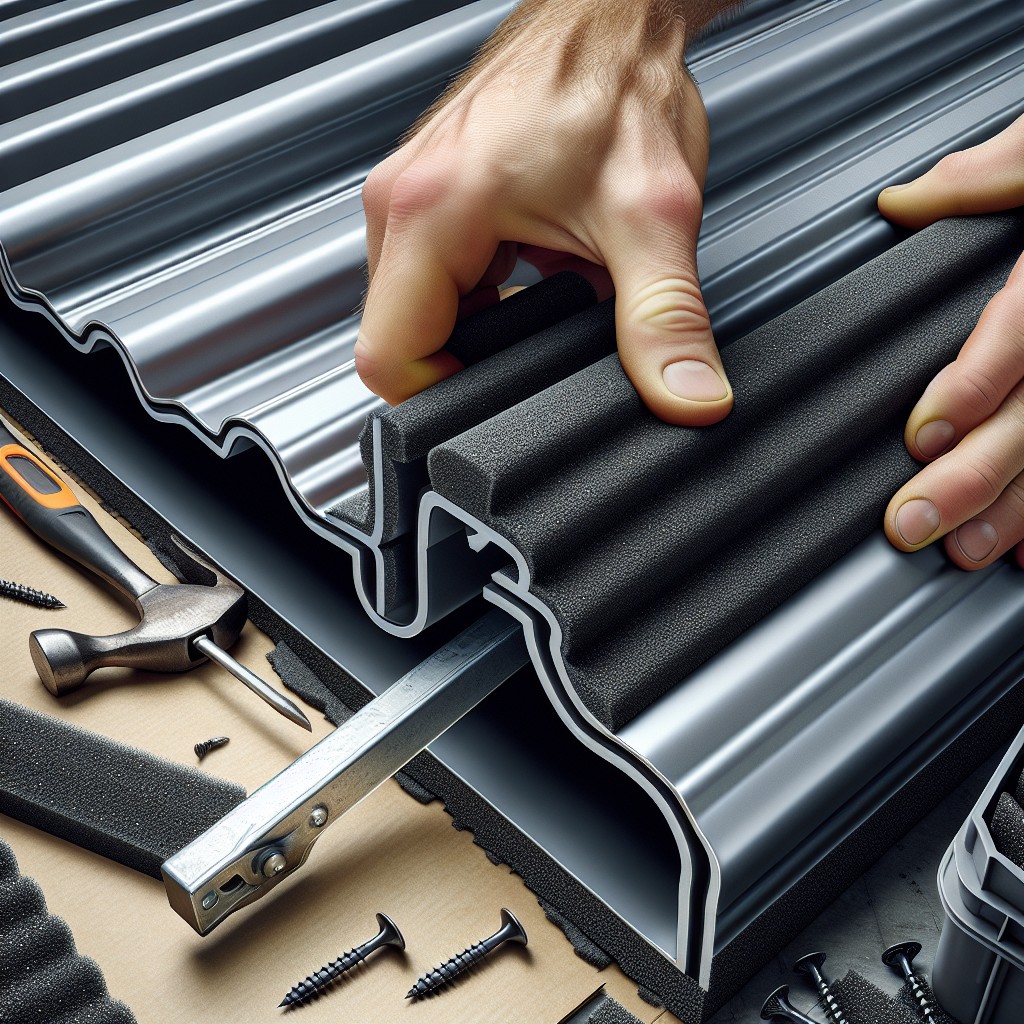
Foam closure strips serve a multifunctional role in the proper installation of metal roofing systems. Their primary function is to create a secure seal between the ridges of metal roof panels and the roof deck or structure. This seal prevents various elements such as water, wind, dust, and pests from infiltrating the roofing system.
By filling in gaps where the roof panels meet underlying structures, these strips mitigate the risk of moisture accumulation that could otherwise lead to corrosion, mold, and structural damage. They also help to maintain consistent temperature regulation by preventing drafts, thereby contributing to the overall energy efficiency of a building.
Furthermore, foam closure strips contribute to the aesthetic finish of a metal roof by providing a uniform appearance. They ensure that the roof panels sit flush against the structure, reducing the possibility of unevenness and vibration that might otherwise cause increased noise levels during windy conditions or rain.
Types of Foam Closure Strips
Foam closure strips come in two primary variations: solid and vented.
Solid strips create a full seal between the roof panels and structure, crucial for preventing water, dust, and pests from entering the building envelope. They match the metal roofing profile and are placed along the eave and ridge ends, complementing the roof’s pitch and peaks.
Vented strips, on the other hand, encourage air circulation, a key factor in maintaining attic ventilation and moisture control. These are typically installed at the ridge where hot air and moisture escape.
Both types are made of durable, weather-resistant materials, such as polyethylene or neoprene, ensuring they hold their shape and effectiveness over time. It’s essential to choose the type that aligns with the specific needs of the roofing system and climatic conditions.
When selecting closure strips, consider compatibility with the metal roofing profile and the intended purpose—either to seal or to ventilate—ensuring optimal functionality of the roofing system.
The Role of Foam Closure Strips in Sealing and Insulation
Foam closure strips serve a dual function in metal roofing systems. Firstly, they create a tight seal between the roof panels and the structure. This seal plays a critical role in preventing water, dirt, and pests from infiltrating the roof. The custom-fit design of these strips fills gaps that would otherwise be susceptible to the elements, ensuring no part of the roof is left unprotected.
Secondly, these strips contribute to the overall insulation of the roof. By sealing off gaps, they help maintain the internal temperature of a building, reducing energy costs by limiting heat transfer. During the warmer months, they prevent hot air from entering, and in cooler months, they trap heat inside, promoting energy efficiency.
In metal roofing, where contraction and expansion due to temperature changes are common, the flexibility of foam closure strips is essential. They adapt to the shifting panels, maintaining the seal and insulation over time. A correctly installed closure strip system enhances your roof’s performance and durability, making it a small but crucial component of the roofing structure.
Installation of Foam Closure Strips
When installing foam closure strips, precision is key to ensure a waterproof and durable metal roof. Start by placing the strips along the eave edges and under the roofing panels. This allows the strips to contour to the panel profile, creating an effective seal against weather elements. Secure the strips using a high-quality adhesive recommended by the strip manufacturer, which helps anchor them in place and prevents wind uplift.
For the ridge or peak of the roof, closure strips should also match the panel configuration for a snug fit. Once the metal panels are laid over the strips, fasten them down through the closure strip to maintain an unbroken seal and keep moisture, insects, and debris out.
It’s important to check that all strips are aligned properly with the panels’ edges, as any misalignment can lead to leaks or diminished insulation properties. Lastly, while cutting strips to fit certain roof dimensions is sometimes necessary, avoid stretching them as this can compromise their sealing capabilities. Always adhere to the installation guidelines provided by the manufacturer for the best results.
Factors to Consider When Selecting Foam Closure Strips
When selecting foam closure strips for a metal roof, evaluate the profile of your metal panels to ensure a snug fit. The material composition of the closure strips is crucial; polyethylene and neoprene are common choices known for durability and water resistance.
Consider the climate in which the roofing will be installed; high UV exposure and temperature fluctuations necessitate UV-resistant and thermally stable strips. Additionally, opt for strips with a strong adhesive backing to facilitate easy installation and create a secure bond to the metal surface.
Lastly, verify compatibility with any sealants or coatings used on the metal roofing to prevent material degradation and ensure long-term effectiveness.
The Longevity and Maintenance of Foam Closure Strips
Foam closure strips, typically made from polyethylene or polyurethane, are designed to withstand the elements in tandem with metal roofing materials. Their lifespan generally aligns with that of the metal roof panels, often ranging from 20 to 50 years. Nevertheless, their durability is influenced by various factors including UV exposure and temperature fluctuations which can cause the material to degrade over time.
To maintain the integrity of the closure strips, it’s important to inspect them periodically, especially if your roof is subjected to extreme weather conditions. Any signs of cracking, shrinking or loss of shape should be addressed promptly to prevent moisture, wind, or pests from compromising the roof structure. If deterioration occurs, replacing the affected closure strips is a straightforward process, typically involving the removal of adjoining panels.
When considering maintenance, ensuring compatibility between the closure strip material and the sealants used on the metal roofing system is crucial. Using non-compatible products can lead to chemical reactions that may shorten the lifespan of the strips. Additionally, proper initial installation is key to maximizing the longevity of closure strips, helping to create a lasting barrier against the elements.
Addressing Common Questions
Metal roofing enthusiasts often present queries centered around the necessity of foam closure strips. To shed light on these inquiries, it’s essential to grasp that while metal roofs can be installed without foam closure strips, their absence can lead to a slew of issues. The strips provide a snug fit for the metal panels, preventing elements such as water, wind, and pests from penetrating the roof structure. This element is particularly crucial in areas prone to severe weather conditions.
Another frequent question pertains to the lifespan of foam closure strips. Typically matching the lifetime of the metal roof panels themselves, these strips are designed to endure. However, it’s important to note that extreme climates and temperature fluctuations can affect their durability.
Choosing the right closure strips involves considering specific roof panel profiles and environmental factors. For instance, ventilated closure strips are optimal for roofs requiring airflow to prevent condensation, highlighting that functionality should be prioritized over cost. Thus, proper selection and installation can significantly enhance both the performance and longevity of your metal roofing system.
Do I Really Need Foam Closure Strips?
The necessity of foam closure strips is often determined by the specific needs of your roofing project. Their primary function is to match the profile of the metal roofing panels, providing a tight seal against weather elements. This helps to prevent water, wind, dust, and pests from entering the ridges and valleys of your roof.
If your building is in an area prone to harsh weather, foam closure strips become essential for adding an extra layer of protection. They also aid in reducing noise from rain or hail and prevent ‘chatter’ — the rattling noise metal roofs can make in high winds.
Additionally, foam closure strips can improve the overall energy efficiency of a building by assisting with proper ventilation and insulation. If reducing energy costs is a priority, these strips can contribute to maintaining a consistent temperature, thus lessening the demand on heating and cooling systems.
While not every metal roofing installation will require foam closure strips, overlooking these components can lead to potential damages and increased maintenance costs over time. It is beneficial to assess the environmental conditions and long-term performance expectations when deciding on the inclusion of closure strips in your roofing system.
How Long Do the Foam Closure Strips Last?
Foam closure strips are designed to endure the elements, often mirroring the lifespan of the metal roofing itself with proper installation and maintenance. They can last anywhere from 20 to 30 years, depending on the quality of the material and exposure to harsh weather conditions.
Ultraviolet (UV) radiation from the sun can degrade the strips over time, causing them to become brittle and less effective at sealing. To bolster longevity, opt for strips treated with UV inhibitors.
Environmental factors, such as extreme temperatures, can also impact durability, so choosing the correct type for your climate is crucial.
Regular inspections are recommended to identify and replace closure strips that show signs of wear to maintain roof integrity.
FAQ
Can you install metal roof without furring strips?
No, installing a metal roof without furring strips is not advisable due to the risk of condensation build-up, which can lead to mold, mildew, and structural damage.
What is a closure on a metal roof?
A closure on a metal roof is a component that fills the space between the base of the roof and the higher portion of the metal panel, varying in design to fit specific roof structures.
Are closure strips necessary for suntuf?
Yes, closure strips are necessary for Suntuf, as they are a part of the complete system intended for optimal installation and warranty fulfillment.
Are foam closure strips a universal fit for all metal roofs?
No, foam closure strips are not a universal fit for all metal roofs as they are designed to match specific profile shapes.
What issues can arise from improper installation of closure strips?
Improper installation of closure strips can lead to severe leaks, increased energy costs, and compromised roof integrity.
What alternatives exist if you’re unable to source closure strips for your metal roof?
If you’re unable to source closure strips for your metal roof, alternatives include using foam closure strips, cut-to-fit insulation, or custom flashing for sealing gaps and preventing leaks.