Last updated on
The durability of TPO roofing has become an intriguing topic for many homeowners, largely because it can greatly influence cost and maintenance plans.
Key takeaways:
- TPO roofing typically lasts 22 to 30 years.
- Factors such as installation quality and environmental conditions affect TPO roof lifespan.
- Regular maintenance extends the life of a TPO roof.
- Weather conditions like UV exposure and temperature fluctuations impact TPO roof durability.
- Proper installation techniques and regular inspections enhance TPO roof longevity.
Average Lifespan of TPO Roofing
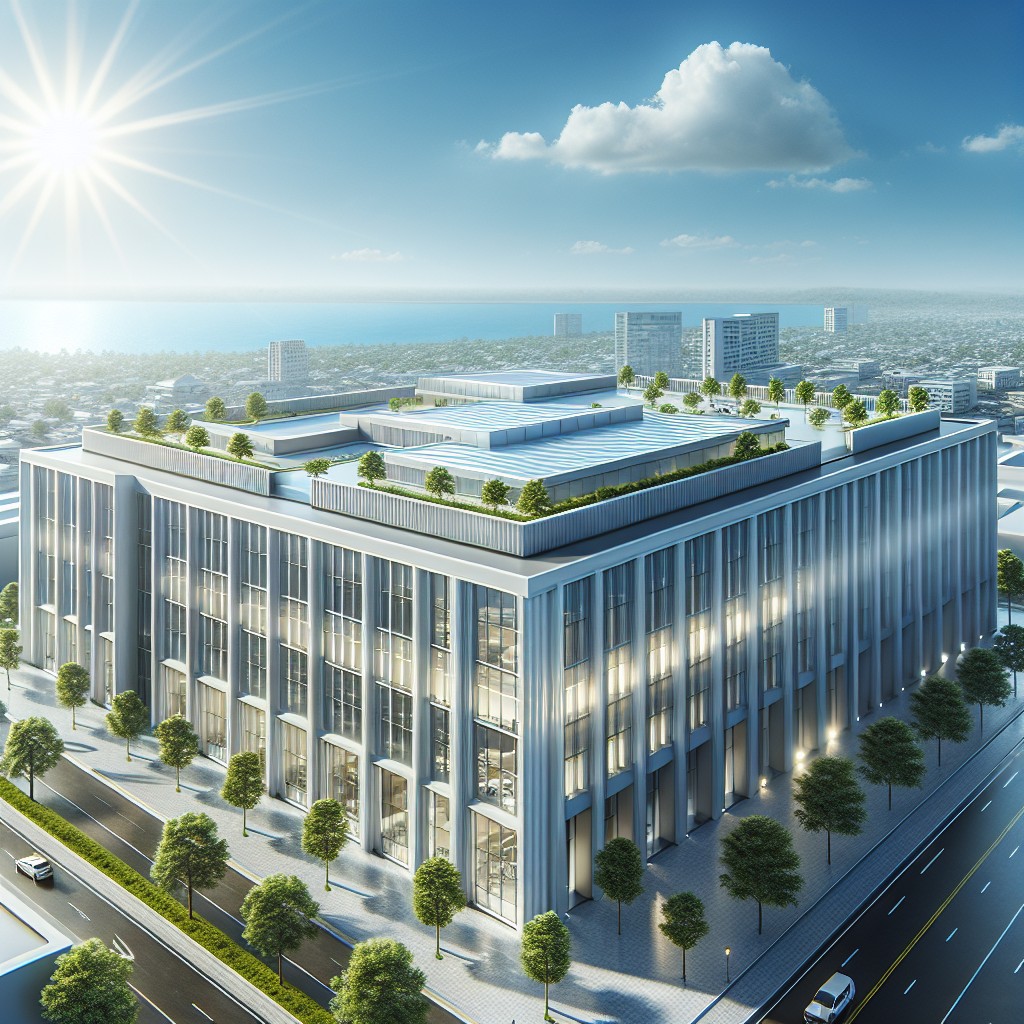
TPO roofing, a popular choice for commercial and industrial buildings, typically offers a service life between 22 to 30 years. Its thermoplastic nature allows it to resist UV radiation, ozone, and chemical exposure, contributing significantly to this lifespan.
The material’s heat-welded seams create a strong bond that mitigates leaks and enhances durability. It’s important to note that the longevity of TPO roofs can be influenced by several factors including installation quality, building design, and environmental conditions.
Regular maintenance can help catch and rectify small issues before they develop into larger problems that could potentially shorten the roof’s lifespan. With attention to these considerations, TPO roofing can provide reliable, long-term performance.
Factors That Determine the Lifespan of TPO Roofs
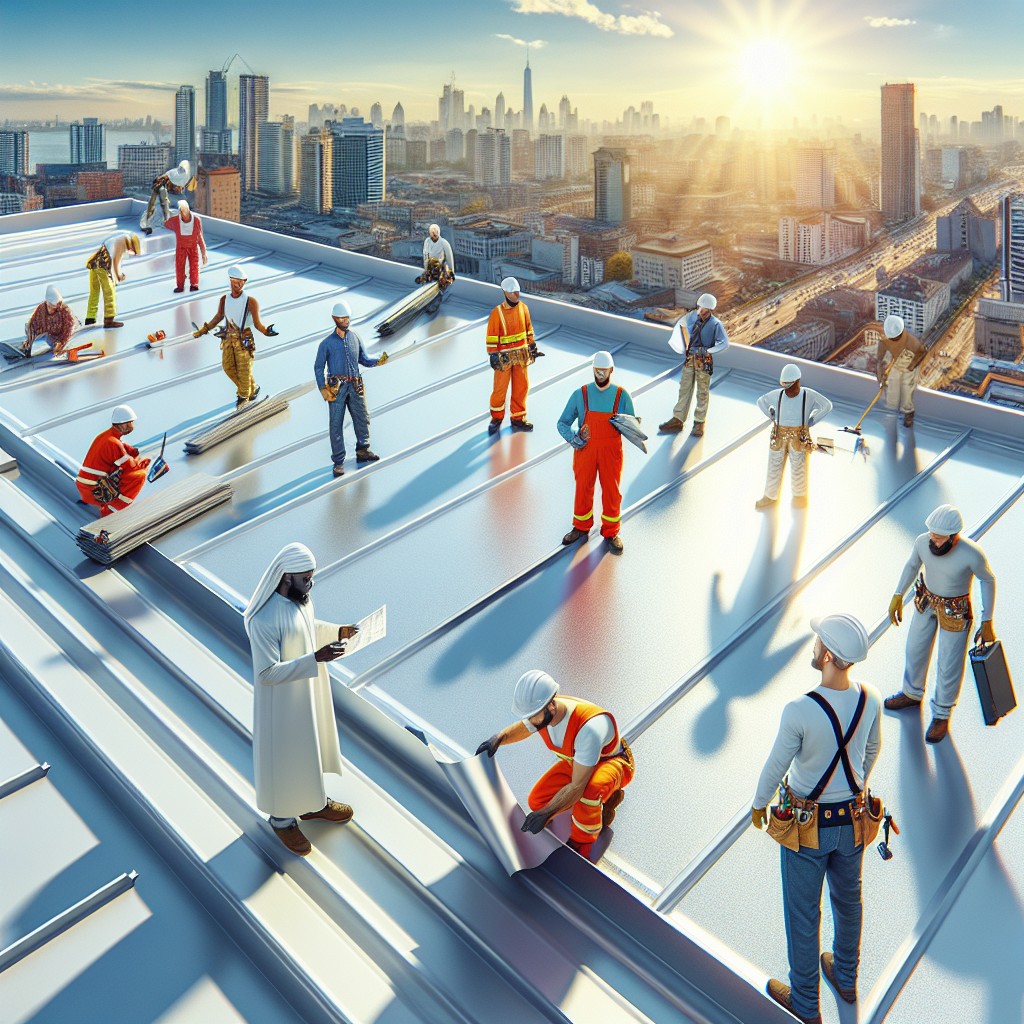
Several variables critically influence how long a TPO roof will perform optimally. The quality of the TPO membrane is paramount; higher-grade materials can withstand weathering and stress better than lower-quality alternatives. Thickness plays a role too—the thicker the membrane, typically, the longer it will endure.
Installation expertise cannot be undervalued. A well-executed installation by experienced professionals ensures seams are properly welded and the roof is correctly attached, mitigating future issues.
Maintenance frequency also matters. Regular cleaning, prompt repairs, and annual inspections help to prevent minor issues from escalating into major problems.
Furthermore, environmental factors such as UV exposure, temperature fluctuations, and harsh weather conditions impact longevity. High UV areas can accelerate the aging of TPO membranes, while severe weather can cause physical damage.
Lastly, building design and usage influence wear and tear. For instance, roofs with high foot traffic may deteriorate quicker than those without.
Understanding these factors is key to maximizing the lifespan of a TPO roof.
Proper Installation Techniques and Their Impact On TPO Roof Longevity
The longevity of a TPO (thermoplastic olefin) roof heavily depends on the quality of the installation. Here are key points illustrating how installation techniques influence roof lifespan:
1. Seam Integrity: TPO membranes are heat-welded at seams. A skilled installer will ensure that seams are welded properly, creating a watertight bond that resists leaks and weathering.
2. Membrane Attachment: There are two primary methods: mechanically attached systems and fully adhered systems. Each has its own set of guidelines that, when followed meticulously, prevent premature failure of the roof.
3. Flashing Installation: Flashing around edges, vents, and equipment is critical for preventing water penetration. Accurate installation helps prevent uplift and water ingress, which can compromise roof integrity.
4. Insulation and Underlayment: Appropriate installation of insulation and underlayment is crucial for ensuring that the TPO membrane lays flat and performs effectively, avoiding issues such as water ponding.
5. Manufacturer’s Guidelines: Compliance with the manufacturer’s specifications is vital. It ensures that all components of the roofing system are compatible and function as intended.
By paying close attention to these elements during installation, you enhance the durability and functionality of a TPO roofing system.
Role of Regular Maintenance in Extending TPO Roof Life
Regular maintenance plays a crucial role in maximizing the performance and longevity of a TPO roofing system. To ensure the roof remains in optimal condition, consider these essential practices:
1. Debris Removal: Keep the surface clear of leaves, branches, and other debris that can accumulate and retain moisture, leading to mold or algae growth.
2. Seam Inspections: Periodically check seams and flashings, as these are common points for leaks to develop. Promptly addressing any issues can prevent more significant problems.
3. Surface Cleaning: Gentle cleaning to remove dirt and environmental pollutants will prevent damage to the TPO membrane and keep it looking new.
4. Minor Repairs: Tend to small punctures, tears, or areas of wear immediately to prevent water infiltration and subsequent damage to the underlying roof structure.
5. Drainage Systems: Ensure drains and gutters are free of blockages so that water can flow freely and not pool on the roof, which can degrade the membrane over time.
Implementing these maintenance steps regularly can effectively extend the service life of a TPO roof, ensuring it provides reliable protection for years to come.
Effects of Weather Conditions On TPO Roof Durability
TPO roofing, known for its heat-reflective properties and resistance to UV radiation, performs well in various climates. However, extreme weather can affect its longevity.
Heat Expansion: High temperatures cause TPO membranes to expand. Although designed for flexibility, prolonged heat can lead to accelerated aging if the roof is not properly ventilated.
Cold Brittleness: In cold climates, TPO remains flexible to a certain point. Below this threshold, the material can become brittle, increasing the risk of cracking under impact.
UV Exposure: Consistent exposure to intense sunlight may degrade the membrane over time, leading to shrinkage and seam issues. TPO’s inherent UV resistance mitigates this risk, but it’s crucial to ensure the roofing grade is suitable for the local UV index.
Wind Uplift: Strong winds can test the integrity of the roof’s installation. Securely welded seams are pivotal in preventing wind from getting under the membrane and causing damage.
Precipitation and Ponds: TPO is waterproof, but standing water can lead to algae growth and membrane degradation if not properly drained.
By understanding the interplay between TPO roofing and diverse weather conditions, one can take preventive measures to safeguard the roof’s integrity and ensure its life expectancy aligns with manufacturer promises. Regular checks and maintenance adapt to local weather patterns are essential in mitigating these effects.
Importance of Roof Inspections for TPO Roofing Systems
Regular inspections are a key component in ensuring the longevity of TPO roofing systems. During these evaluations, professionals look for signs of wear and tear, such as seam integrity, membrane thinning or punctures, and flashing details that may have become compromised.
Prompt identification of these issues can lead to immediate repairs, thus preventing water infiltration and more extensive damage. Typically, biannual inspections are recommended – once before the harsh weather season to prepare the roof, and once after to assess any impacts.
Additionally, checking for the accumulation of debris and the functionality of drainage systems during inspections can prevent water ponding, which can otherwise lead to accelerated aging of the TPO membrane. By prioritizing these inspections, the performance of a TPO roof can be optimized, potentially exceeding its expected service life.
Repair and Restoration Options for Aging TPO Roofs
When TPO roofs near the end of their service life, addressing issues promptly can prevent premature replacement. Small punctures or tears can often be welded shut or patched using compatible materials. It’s critical to clean the affected area thoroughly before applying these repairs to ensure proper adhesion and a long-lasting fix.
Restoration, as an alternative to total replacement, can significantly extend the lifespan of a TPO roof. Restoration procedures typically involve the application of a roof coating after a comprehensive cleaning. Acrylic or silicone-based coatings are popular choices that provide an additional layer of protection against UV rays, weathering, and leaks.
Outdated or damaged flashing and seams represent common problems for aging TPO roofs. In such cases, a professional may re-weld seams or replace flashing to maintain the roof’s integrity. Ensuring that these critical junctions are secure helps prevent water infiltration and structural damage.
For building owners considering restoration methods, it’s essential to consult with professionals. They can assess the roof’s condition and recommend specific restoration techniques tailored to the TPO material, factoring in the roof’s age, current state, and the owner’s budget.
Lastly, maintenance combined with repairs can transform an aging roof. A holistic approach that includes regular inspections and immediate attention to small issues can sustain a watertight and functional roofing system before a full-scale replacement is necessary.
Methods to Enhance the Performance and Lifespan of TPO Roofing
Ensuring optimal performance and extending the service life of a TPO roof can be achieved through several proactive strategies:
1. Regular Cleaning: Debris and dirt can accumulate on the roof surface, leading to punctures and membrane degradation. Periodic cleaning helps avoid these issues.
2. Seam Maintenance: Over time, seams may become weak points. Regular inspection and reinforcement, using quality seam adhesives, prevent leaks and separation.
3. Minimizing Foot Traffic: While TPO roofs can withstand some foot traffic, limiting unnecessary access helps prevent abrasions and membrane damage.
4. Prompt Repairs: Addressing minor issues immediately can prevent them from escalating into major problems, thereby safeguarding the roof’s integrity.
5. Ultraviolet Protection: The application of reflective coatings can reduce UV radiation impact, slowing the aging process and contributing to energy efficiency.
6. Proper Insulation: Adequate insulation improves thermal performance and reduces the thermal cycling that can lead to TPO membrane fatigue.
Comparison of TPO to Other Commercial Roofing Materials
TPO roofing, known for its heat-reflective properties, stands out among other options for its energy efficiency. Compared to EPDM, another popular single-ply roofing membrane, TPO is more resistant to punctures and offers a cleaner, welded seam that is less prone to leakage.
Unlike PVC roofing, TPO does not contain chlorine, a feature that may be preferred for environmental considerations.
Meanwhile, metal roofing boasts a longer lifespan but at a higher installation cost and potential for noise during rain or hail.
For those assessing costs, built-up roofing (BUR) and modified bitumen are generally less expensive upfront but may require more maintenance over time, potentially diminishing their overall value compared to TPO’s longer-term performance and lower energy costs.
TPO Warranty: Understanding the Fine Print and Its Implications
When assessing TPO roofing warranties, it’s critical to scrutinize the details to ensure a clear understanding of what is covered and for how long. Manufacturer warranties typically range between 10 to 30 years and usually cover defects in the roofing membrane itself. However, this does not automatically include labor or installation errors. On the other hand, a workmanship warranty provided by the roofing contractor may cover installation but is often for a shorter period.
Key points to consider in TPO roofing warranties include:
- Types of Coverage: Understand the difference between a “material-only” warranty, which covers only the membrane, and a “full system” warranty, which encompasses the membrane and other components used in the installation.
- Prorated vs. Non-Prorated: Some warranties are prorated, reducing the coverage value over time, while non-prorated warranties offer full coverage for the duration of the warranty period.
- Exclusions: Warranties may have exclusions for certain types of damages, such as punctures, standing water, or damages from rooftop equipment.
- Maintenance Requirements: Regular maintenance may be required to keep the warranty valid; neglecting this can void the warranty.
- Transferability: If the property changes ownership, check if and how the warranty can be transferred to the new owner.
Understanding these terms ensures that you are well-informed about the warranty protection for your TPO roof and can take proactive steps to maintain its coverage over time.
FAQ
How long does a residential TPO roof last?
A residential TPO roof typically lasts between twenty to thirty years.
What are the cons of TPO roofing?
One of the disadvantages of TPO roofing is that, after years of wear and tear, it may require leak repair.
How durable is TPO roofing?
TPO roofing is highly durable due to its hot air welded seams, which are three times stronger than those of conventional rubber roofs using tape systems and six times stronger than roofs with glued seams.
How do you extend the life of a TPO roof?
To extend the life of a TPO roof, utilize silicone or acrylic coating systems which efficiently restore and increase the roofing system’s durability.
What maintenance is required for a TPO roof?
A TPO roof requires regular cleaning, seam inspection, and professional maintenance to fix punctures, blisters, or cracks annually or after severe weather.
How is a TPO roof’s lifespan affected by weather conditions?
Extreme weather conditions, like intense sunlight or freezing temperatures, can accelerate the wear and tear on a TPO roof, potentially shortening its expected lifespan of 15 to 20 years.
What signs indicate a TPO roof might need replacement?
Signs indicating a TPO roof might need replacement include consistent leaks, blisters or cracks on the surface, pooling water, and a worn-out or faded appearance.