Last updated on
From flash floods to violent blowing storms, water damage is a major threat to the structural integrity of industrial buildings. This threat is magnified in the era of climate change. It is becoming increasingly common for regions to get hit with unexpected storms and receive a year’s worth of precipitation in just a few days.
As such, it is crucial for modern commercial architects to design with moisture protection in mind. Keep reading as we explore water resistive systems and other moisture safeguards for industrial buildings.
What Is a Water Resistive System?
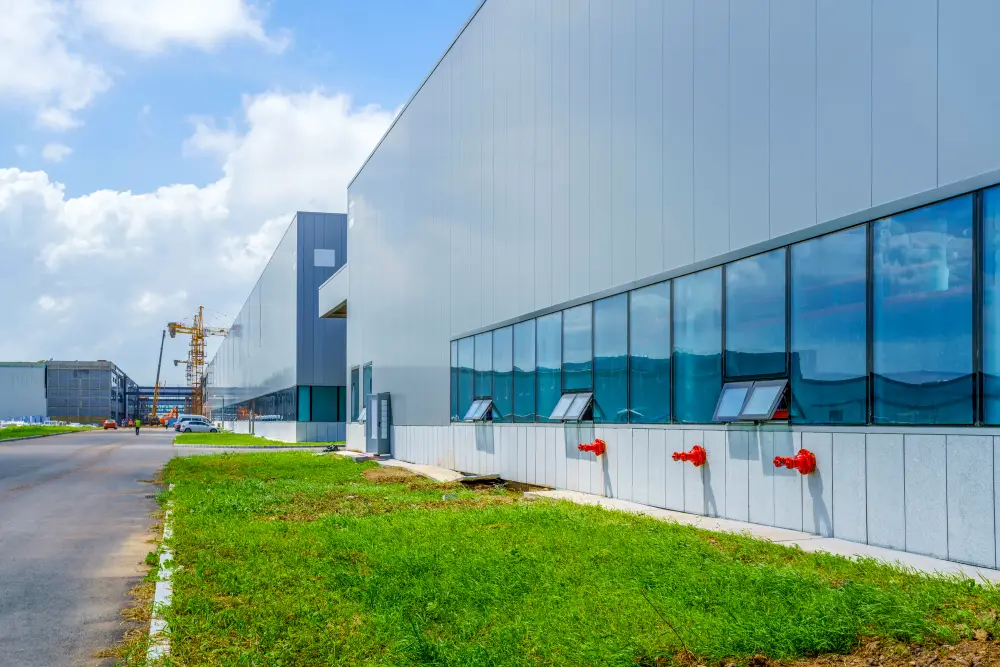
A complete water resistive system includes cladding that protects the exterior of the building from bulk water infiltration and a water resistive barrier assembled between the cladding and exterior sheathing. This type of barrier is generally made from spun bonded polyolefin or engineered fabric and it resists water that leaks, penetrates, or seeps past the initial cladding layer.
This keeps water from infiltrating the building interior. The success of a water resistive barrier depends on the correct, continuous configuration of interconnected details, especially at key intersectional points, such as window-to-wall or roof-to-wall transitions.
Key Moisture Safeguards for Industrial Buildings
As mentioned, the correct application of water resistive barriers–commonly referred to as “building wrap”– is a crucial component of a water resistive system. However, there are numerous other safeguards in industrial building construction that are necessary to protect the structure against moisture damage.
Moisture protection for an industrial building begins with the foundation. Liquid flashing is a common protective measure that keeps moisture from seeping into foundation concrete. However, it may not be adequate enough in areas that experience high hydrostatic pressure in the groundwater. More complete foundation waterproofing involves applying a fully-adhered membrane to the foundation walls.
This membrane allows water to pass and directs it to a drainage mat, which then moves the water to a subterranean pipe system and away from the structure. This guarantees that heavy below-ground water pressure does not erode the area housing the foundation, promoting the ongoing health of the building.
Fortified Framing
While water resistive barriers go a long way toward keeping water from ever reaching the framing, the framing materials themselves are just as important for preventing moisture damage in the structure. As such, oriented strand board (OSB) framing is not the preferred framing solution for moisture protection.
OSB framing often involves a series of minor imperfections that can allow water ingress without the proper sealants. In addition, the OSB itself may absorb water, causing swelling and shrinkage that can cause a number of complications for structural walls.
More extensive water exposure can also lead to rot, mold, and mildew concerns. For most commercial applications, insulated concrete forms (ICF) and steel beams are preferred framing solutions, thanks to their impermeability.
Adequate Insulation
In addition to its role in improving R-value and stabilizing interior temperatures, insulation is also a key component of mitigating water damage. Spray foam insulation is a commonly used product in structural steel buildings that does an admirable job of limiting moisture ingress.
Furthermore, commercial water pipe insulation helps maintain fluid temperature to protect pipes from the damage caused by freezing and excess temperatures, helping keep the industrial building free from expensive and inconvenient commercial pipe leaks.
Water-resistant Roofing
Commercial roofs are often flat and must be able to accommodate additional weight and traffic over the typical residential roof. Without the proper substrate, flashing, roof curb, and surface materials, commercial roofs are at high risk of developing leaks.
Special attention should be given to the intersection of flat roofs and vertical walls. In order for these interfaces to be completely water resistive, they must employ continuous and properly lapped coping over the roof and walls to keep bulk water out of the building enclosure.
It should also include a correctly lapped secondary barrier in the event that coping joints fail and allow water infiltration. To complete the water-resistive setup, drip edge flashing helps direct drained water away from the building.
Upgraded Windows
Similar to roof-to-wall transitions, window apertures are another notorious location for moisture infiltration in a commercial building. Damaged glass and degraded frames offer the path of least resistance for interior/exterior pressure differences to correct themselves.
As such, many modern industrial buildings are installing hurricane-grade storm windows to complete a water-resistive infrastructure. Fabricated with structural steel frames and reinforced glass panels, these robust windows offer the highest wind and impact resistance on the market, offering the building top-notch protection amid violent storms and blowing moisture.
Use Water Resistive Systems to Protect Industrial Buildings from Moisture Damage
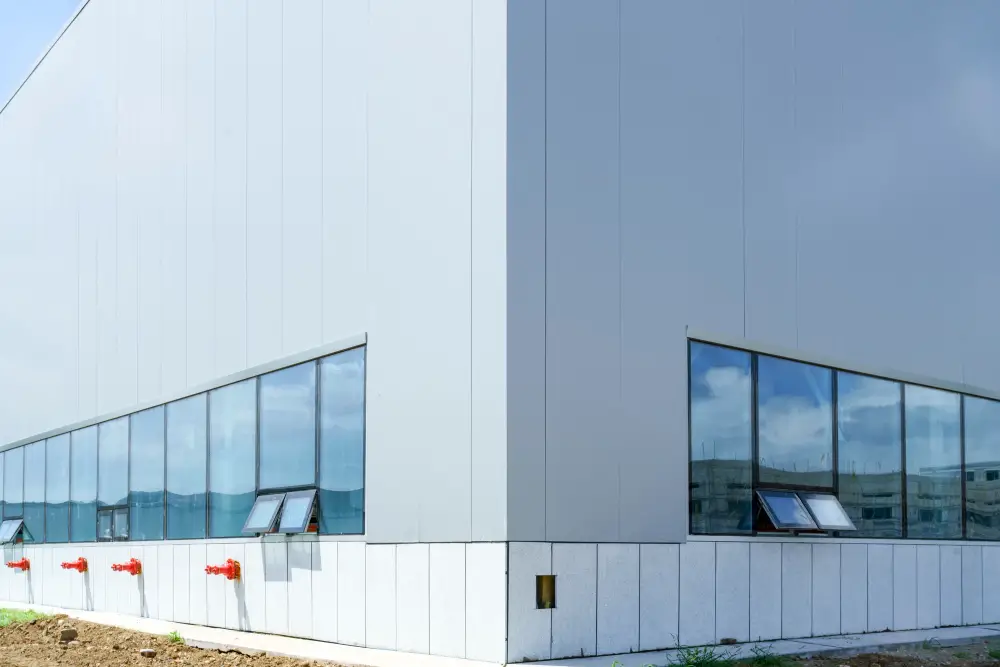
Uncontrolled moisture is a major threat to industrial buildings–a threat that is increasingly magnified in the era of climate change. By considering the implementation of water resistive barriers and the other moisture safeguards listed above, commercial structures can get a leg up in the fight against moisture damage.
For more ideas and insight on water-resistant design, explore Roofer Digest for leading expert tips.